Advantages & Differentiation
BioLogiQ’s Invention
Starch and starch-blended plastics have been available for years and are commonly known as Thermoplastic Starch (TPS) and TPS blends. However, these TPS plastic products have been expensive to produce and have not achieved the level of quality that is required to make high-quality thin films for plastic bags.
BioLogiQ invented a new kind of TPS that it calls iQ (NuPlastiQ BioPolymer.
Using its proprietary process, BioLogiQ’s makes a low moisture content plasticized starch resin pellet called NuPlastiQ. We make NuPlastiQ in pellet form so plastic product manufacturers can use them like other traditional plastic resin pellets using their standard production equipment.
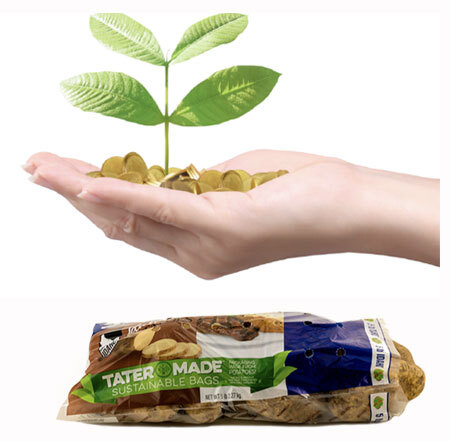
BioLogiQ’s iQ™ (NuPlastiQ®) pellets are designed to be blended with various plastics to make BioBlends that increase the sustainability of the final product.
Most companies that make starch blends today start by blending conventional fossil-fuel plastic resin pellets with starch powder using twin screw compounding machines. The resulting blended pellets are usually not very well mixed and cannot be used to make the same high-quality and high-performance thin films as can be made by using BioLogiQ’s NuPlastiQ pellets. NuPlastiQ can be blended with every type of conventional plastic and also with other bioplastic resins.
At BioLogiQ, we have invented iQ™ Technology, a process that allows us to make blends of NuPlastiQ with traditional low-density polyethylene in such a unique way that the resulting thin films are significantly stronger than the PE-only film structures. This significant breakthrough makes it possible to reduce the thickness of the thin films.
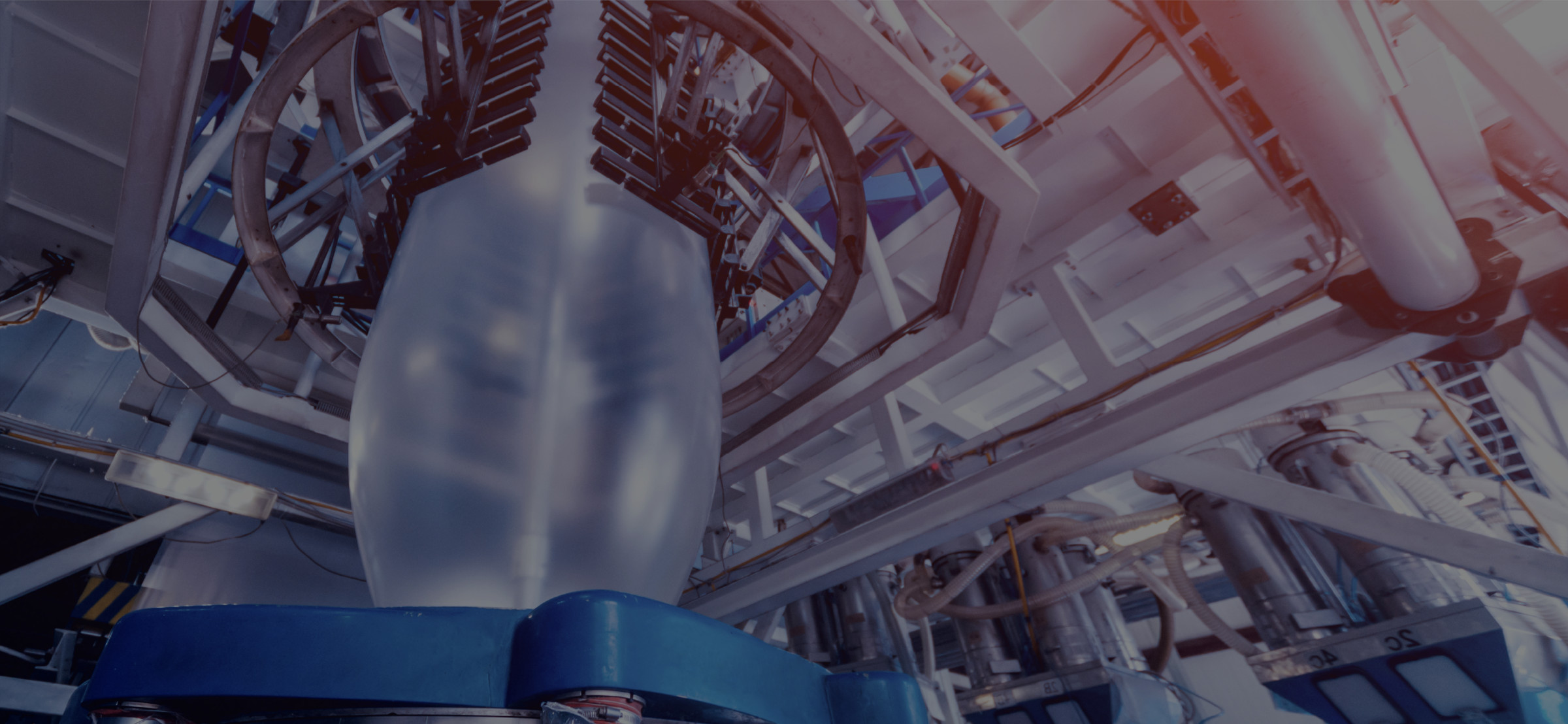
Adding BioLogiQ’s NuPlastiQ to LLDPE or LDPE increases the bubble stability and makes it possible to blow films as thin as .1 mil (2.5 microns)
Bags made with 25% NuPlastiQ and 75% PE that are downgauged by 30% result in 50% less fossil fuel being used to make the bags. This, in turn, reduces the amount of conventional non-biodegradable PE that ends up in landfills and the ocean.
Thinner bags results in lower costs and the adoption of iQ (NuPlastiQ) reduces global warming potential of the blend by up to 50%.
1.
Decouple plastics from fossil-fuel feedstocks
2.
Create an Effective After-use Plastics Economy
3.
Drastically reduce “leakage” of plastics into the environment – Increase use of biodegradable plastics

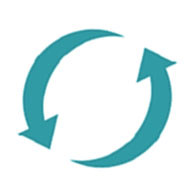
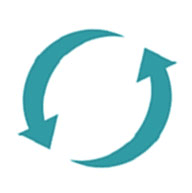
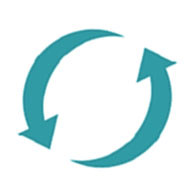
Do you want to get serious about sustainability?
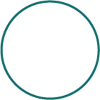
By blending BioLogiQ’s NuPlastiQ with polyethylene to make thin films, we can often achieve an affordable, durable product that is more compatible with nature’s biodegradation* systems, therefore leading to reduced microplastics potential without compromise to performance.
Compostability & Biodegradability
BioBlend BC Resins
NuPlastiQ may be blended with other compostable resins such as PBS, PHA, PBAT or PLA to meet Industrial or Home composting requirements. In its pure form, NuPlastiQ has biodegraded at the same pace of cellulose.
NuPlastiQ and several BioBlend BC grades have passed standardized tests for compostability and are certified by TUV to meet the criteria specified in ASTM D6400 and EN 13432. Some BioBlend BC grades have also passed the China Standard Biodegradability Test GB/T 19277.1-2011.
Working towards making plastics sustainable
BioLogiQ’s NuPlastiQ® BioPolymer is made from annually renewable agricultural resources.
A good way to increase sustainability is to look for ways to reduce the amount of plastic and to reuse and recycle plastic products. The 3 R’s “Reduce, Reuse, Recycle” have been the focus of the plastic industry for the past decade, but that process hasn’t been successful enough, with more than an estimated 11 million tons (by PEW) of plastic estimated to reach the ocean every year.
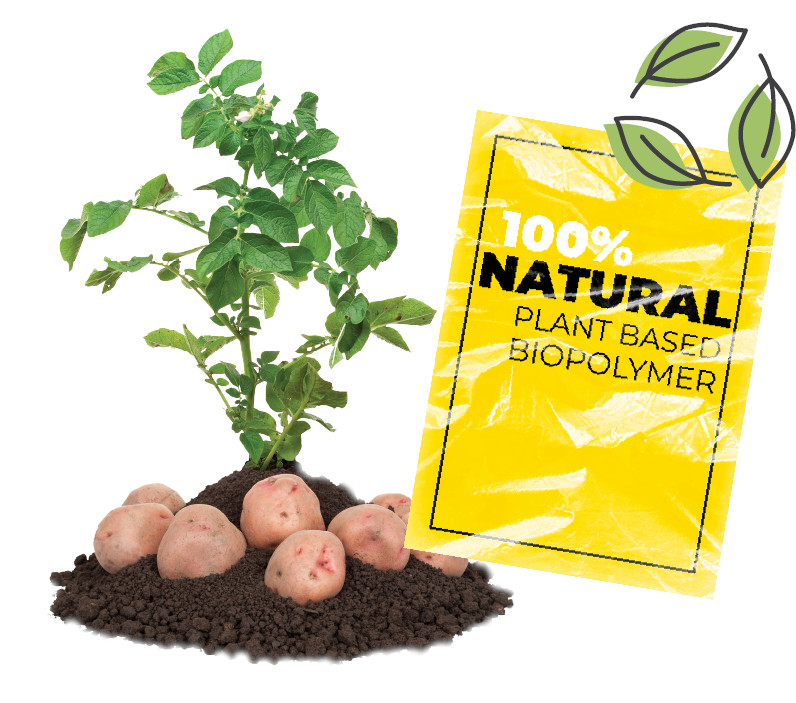
Reduce, Reuse, and Recycle are important parts of the road to a more sustainable future, and BioLogiQ is already innovating its way to solid solutions.
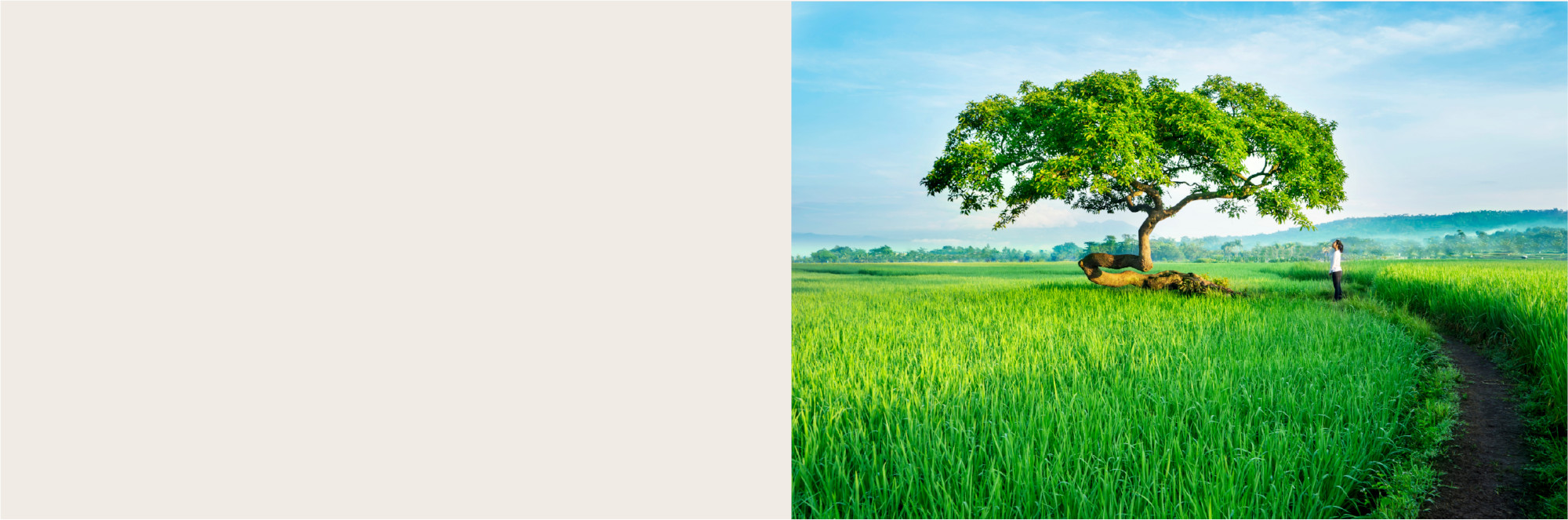
Plant-powered
NuPlastiQ® & its BioBlends®
BioLogiQ is working to improve the path to true circularity through its revolutionary plant-based 100% natural renewably sourced biopolymer called NuPlastiQ.
NuPlastiQ is the natural ally to solving the man-made problem of plastic pollution. NuPlastiQ reduces the accumulation of plastic pollution* in our environment and ocean.
NuPlastiQ is the natural ally to solving the man-made problem of plastic pollution.
Introducing the 4th “R”
Remediation, or Bioremediation
NuPlastiQ® has been designed to help reduce the accumulation of plastic pollution* in our environment and ocean.
We are all familiar with the 3 “R’s” of the environment—Reduce, Reuse, Recycle. NuPlastiQ paves the way for a critical fourth “R” —Remediate—”The process of improving something or correcting something that is wrong, especially changing or stopping damage to the environment.” Applying remediation increases the chance that leaked plastic doesn’t persist. How?
Nature has developed a way to biodegrade durable polymers such as cellulose and lignin. Like wood, plastics may aspire to be durable and compatible with nature’s biodegradation systems. NuPlastiQ seems to enable nature to use its biodegradation* toolbox in blends with PE, PP and PS. A possibility demonstrated in dozens of studies and that does not seem to be accelerating fragmentation. The addition of NuPlastiQ in PE, PP and PS can only reduce the potential for persistent microplastics accumulation in the environment.
Taking A Page From Nature
Copyright © 2021 BioLogiQ, Inc. All rights reserved. Although BioLogiQ, Inc. and its affiliates (“BioLogiQ”) have taken reasonable steps to ensure the accuracy of the information presented in this infographic, BioLogiQ makes no representations or warranties with respect to the information provided herein.
NuPlastiQ® seems to be acting as a bioremediation trigger that enable naturally–occurring microbes to bioremediate plastics lost in the environment.
Meet EBT: Embedded Bioremediation Triggers
Copyright © 2021 BioLogiQ, Inc. All rights reserved. Although BioLogiQ, Inc. and its affiliates (“BioLogiQ”) have taken reasonable steps to ensure the accuracy of the information presented in this infographic, BioLogiQ makes no representations or warranties with respect to the information provided herein.
Biodegradability and Compostability
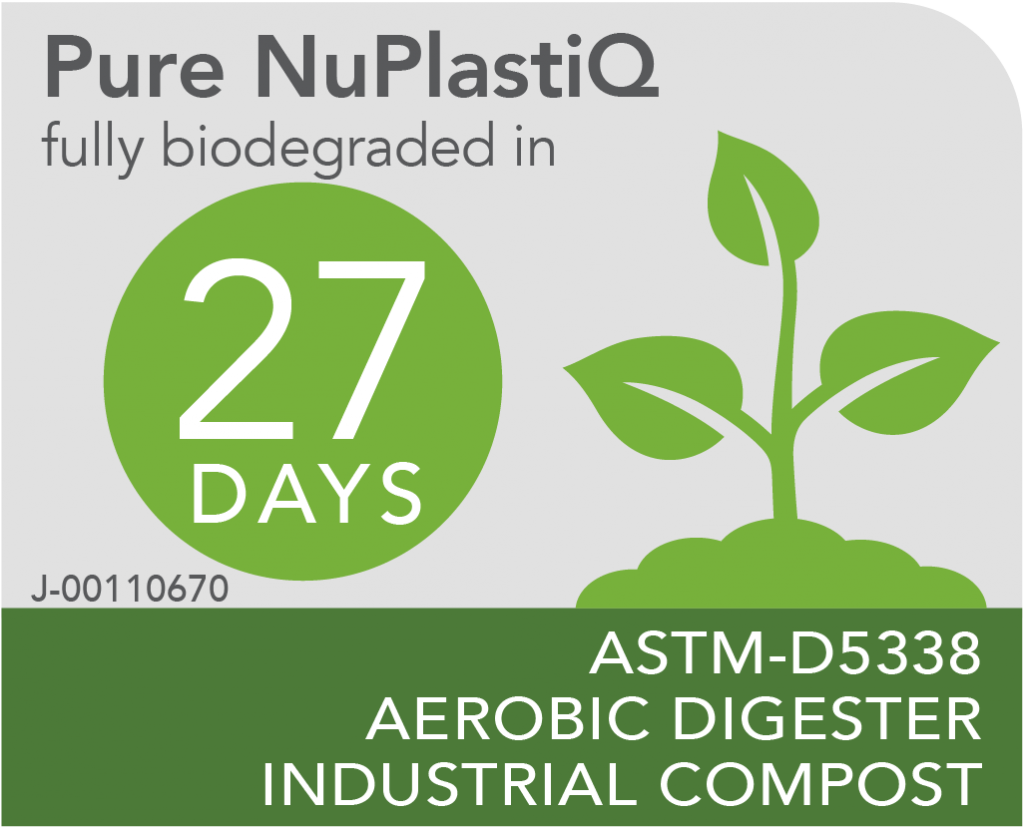
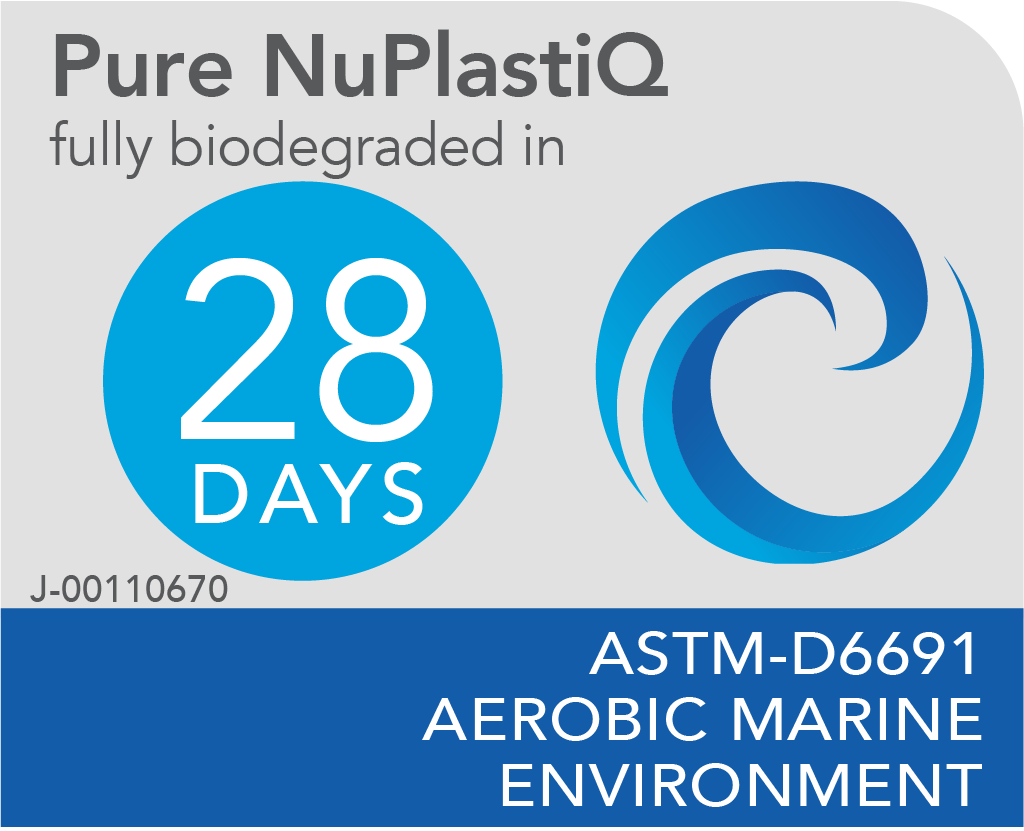
Products made with BioLogiQ’s NuPlastiQ® are durable and shelf-stable. They will not accelerate fragmentation simply because of the presence of oxygen or UV light.
BioBlend BC Resins:
NuPlastiQ will typically accelerate biodegradability of compostable resins such as PBS, PHA, PBAT or PLA, expanding the envelope of certifiable applications. In its pure form, NuPlastiQ has biodegraded as fast as cellulose under ASTM D5338 and D6691.
NuPlastiQ and several BioBlend BC grades have passed standardized tests for compostability and are certified by TUV to meet the criteria specified in ASTM D6400 and EN 13432. Some BioBlend BC grades have also passed the China Standard Biodegradability Test GB/T 19277.1-2011.

Greenhouse Gas (GHG) Savings
At BioLogiQ we are committed to preserving the quality of life we all enjoy here on the planet. Excessive reliance on fossil fuels over the past 100 years has created worldwide concerns about changes in climate, long-lived pollution, and the fact that fossil fuel, in general, is a finite resource.
We make plastic from annually renewable starch (NuPlastiQ resin) rather than petroleum to address the many valid concerns.
Mixing BioLogiQ’s NuPlastiQ BioPolymers resins with any of the petroleum-based plastic resins has dramatic and immediate effects on the carbon emissions (CO2) that ultimately affect the growing “greenhouse gas” problem. Our resins can be used as a “drop-in” replacement for a portion of polyethylene, polypropylene or polystyrene, etc. No special equipment is required for manufacturers to use our resins and there is no increase in labor costs. It simply works.
GHG Savings at a glance:
NuPlastiQ® offers significant GHG savings when blended with fossil-based resins.
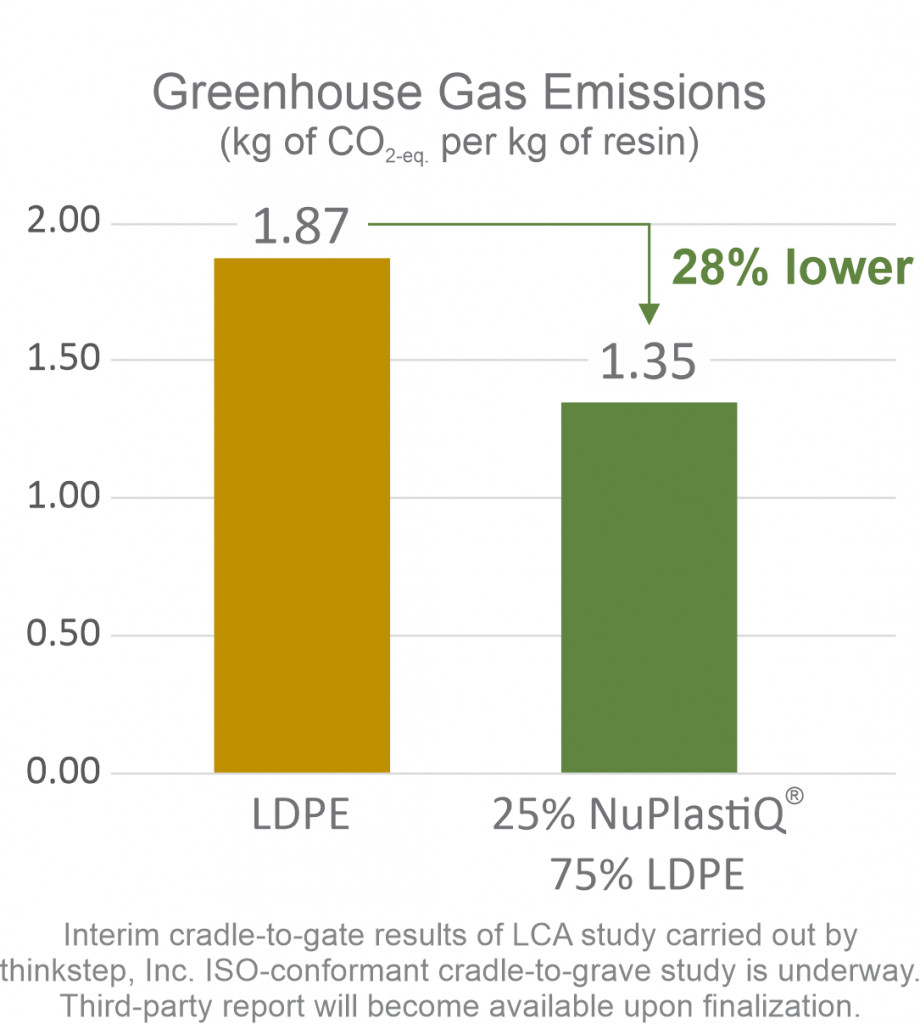
- Thanks to plant-based content and efficient conversion, NuPlastiQ is basically carbon neutral:
- Study carried out by thinkstep, Inc. concluded that NuPlastiQ has a cradle-to-gate carbon footprint of approximately -0.2 kg of CO2-eq. per kg of resin. That includes energy that is required to compound NuPlastiQ with a partner resin.
- Example of a product containing 25% NuPlastiQ (figure to the left)
- Baseline LDPE structure: 1 kg of LDPE with a GWP of 1.87 kg CO2-eq.
- New structure with NuPlastiQ :
- 0.25 kg of NuPlastiQ with a GWP of -0.05 kg CO2-eq. [0.25 x -0.2]
- 0.75 kg of LDPE with a GWP of 1.40 kg CO2-eq. [0.75 x 1.87]
- Total GWP of 1.35 kg CO2-eq. [-0.05 + 1.40]
- Quick way to estimate GHG savings from including NuPlastiQ in a blend:
- For practical purposes, the resin related, cradle-to-gate GHG saving in a blend of NuPlastiQ with a fossil-based material (e.g. LDPE) will be roughly equal to the percentage of NuPlastiQ in the blend
- For practical purposes, the resin related, cradle-to-gate GHG saving in a blend of NuPlastiQ with a fossil-based material (e.g. LDPE) will be roughly equal to the percentage of NuPlastiQ in the blend
Please recognize the limitations of such simplified calculations. While useful to estimate the resin related benefit, they are not inclusive of all factors when a final product is considered: printing inks, label, resin processing energy (e.g. injection molding), etc. Consult an LCA expert prior to LCA-related claims.
For a more detailed explanation of NuPlastiQ’s GHG profile, please continue to the next “In depth” section.
In Depth:
I. NuPlastiQ® is a plant-based thermoplastic. Every carbon in its backbone came from atmospheric CO2.
- Plants use sunlight (light energy) to make “foods” (chemical energy) from carbon dioxide CO2 and water H2O;
- This chemical energy is stored in carbohydrate molecules, such as starches and sugars;
- The basic chemical formula of starch, our primary ingredient for NuPlastiQ, is (C6H10O5)n and its carbon atoms came from atmospheric CO2;
- The same goes for plant-based Glycerin, the other ingredient in NuPlastiQ. With chemical formula C3H8O3, all its carbons came from atmospheric CO2.
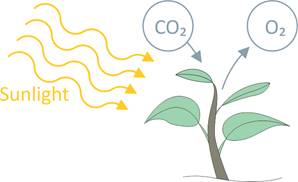
II. CO2 uptake to make one kilogram of NuPlastiQ® :
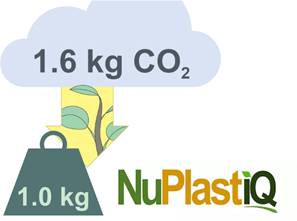
Carbon atoms in one kilogram of NuPlastiQ were absorbed by plants from the atmosphere during photosynthesis as ~1.6 kilograms of CO2.
- 1 kg of NuPlastiQ consists of approximately 440 grams of carbon, 60 grams of hydrogen and 500 grams of oxygen;
- 1 kg of CO2 consists of approximately 273 grams of carbon and 727 grams of oxygen;
- In order to obtain the 440 grams of carbon needed to make 1 kg of NuPlastiQ, ~1.6 kg of CO2 needs to be taken from the atmosphere by plants (440 ÷ 273≈1.6).
Note: If NuPlastiQ is biodegraded at the end of its life, its carbons are returned to the atmosphere in the form of CO2 or the less desirable CH4.
III. CO2 emissions to make one kilogram of NuPlastiQ®:
There’s a lot of work to convert atmospheric CO2 into ready-to-use NuPlastiQ:
Diesel for agriculture, fertilizer production and use-related emissions, energy for starch and NuPlastiQ processing, diesel for transportation, etc.
Interim results of a Cradle-to-Gate Life Cycle Assessment (LCA) study carried out by thinkstep, Inc indicate that such work would amount to ~1.4* kilograms of CO2-equivalent (GWP100) emitted for every kilogram of NuPlastiQ manufactured.
These numbers make NuPlastiQ about carbon neutral at BioLogiQ’s gate.
Carbon-neutrality is excellent. And there seems to be room for improvement with more advantaged sources of glycerin and more energy efficient production methods. We are working on it.
A critically reviewed third-party report will be available upon conclusion of current capacity scale up, with new raw material sourcing points established and ongoing energy efficiency measures implemented.
* 1.4 includes emissions related to compounding of NuPlastiQ with LDPE in a 50/50 BioBlend®. For clarity purposes, CO2-equiv burden of LDPE will be added in the following step.
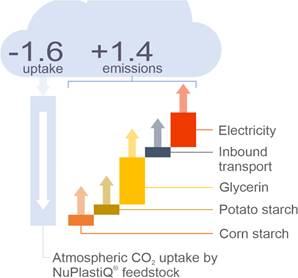
IV. Estimate your potential saving: NuPlastiQ® % ≈ GHG saving % in 1:1 ratio replacement use cases**
As demonstrated above, NuPlastiQ is roughly carbon neutral at BioLogiQ’s gate.
That makes estimating the resin related GHG saving, at your gate, as simple as:
- Learn the “at gate” GWP (Global Warming Potential) value for your base resin from a reputable source, such as https://www.plasticseurope.org/en/resources/eco-profiles.
- E.g. GWP100 for 1 kg of LDPE is listed as 1.87 kg CO2-eq. (GWP100)
- Calculate GWP saving for your use case.
- E.g. 1:1 replacement ratio (by weight), 30% NuPlastiQ blended with 70% LDPE:
- Before: 1 kg of LDPE x 1.87 = 1.87 kg CO2-eq.
- After: [0.3 kg of NuPlastiQ x 0] + [0.7 kg of LDPE x 1.87] = 1.31 kg CO2-eq.
- Net saving: 1- [1.31 ÷ 1.87] = 30% lower resin related GWP at factory gate
- E.g. Final structure 10% heavier for same function, 30% NuPlastiQ blended with 70% LDPE:
- Before: 1 kg of LDPE x 1.87 = 1.87 kg CO2-eq.
- After: [0.33 kg of NuPlastiQ x 0] + [0.77 kg of LDPE x 1.87] = 1.44 kg CO2-eq.
- Net saving: 1- [1.44 ÷ 1.87] = 23% lower resin related GWP at factory gate
- Note: A heavier structure “at gate” will have downstream GWP implications (more energy for transport, etc.). Estimated saving “at gate” will likely be reduced.
- E.g. Final structure 10% lighter for same function, 30% NuPlastiQ blended with 70% LDPE:
- Before: 1 kg of LDPE x 1.87 = 1.87 kg CO2-eq.
- After: [0.27 kg of NuPlastiQ x 0] + [0.63 kg of LDPE x 1.87] = 1.18 kg CO2-eq.
- Net saving: 1- [1.18 ÷ 1.87] = 37% lower resin related GWP at factory gate
- E.g. 1:1 replacement ratio (by weight), 30% NuPlastiQ blended with 70% LDPE:
- Get an idea of what the saving represents by using comparative tools such as EPA’s “Greenhouse Gas Equivalencies Calculator“.
- E.g. 30% NuPlastiQ, 1:1 by weight, 100 metric tons of packaging per year
- Before: 100,000 kg of LDPE x 1.87 = 187 metric tons of CO2-eq.
- After: [30,000 kg of NuPlastiQ x 0] + [70,000 kg of LDPE x 1.87] = 131 metric tons of CO2-eq.
- Net saving: 187 – 131 = 56 metric tons of CO2-eq. per year (resin related GWP at factory gate)
- EPA’s tool calculated GHG equivalency (Aug 5th 2019): 19.5 metric tons of waste recycled instead of landfilled per year.
- E.g. 30% NuPlastiQ, 1:1 by weight, 100 metric tons of packaging per year
Note: Please recognize the limitations of these simplified calculations. While useful to estimate resin related benefits, they do not include all elements needed to calculate the GWP of a final product: printing inks, label, resin processing energy (e.g. injection molding), etc. Consult an LCA expert prior to making GHG-related claims.
** when blending NuPlastiQ to fossil-based resins. 1:1 replacement ratio by weight. Comparison of ready to use resin blend at factory’s gate.
V. What do resin related GHG differences look like “beyond the gate”?
Now things can get really complex, really fast! So to simplify, we are limiting our comparisons to LDPE.
- The below analysis is limited to emissions directly related to the different plastic resin blends;
- Emissions related to transport beyond manufacturers’ gates, resin processing into packaging or final product, etc. are out of scope since they are expected to be very similar irrespective of the different resin blends;
- For the purposes of this analysis, it is assumed that different resin blends perform exact same function until the use stage;
- It is known that different resin blends may behave differently at the end-of-life. GHG differences may be relevant;
- Additionally, different end-of-life treatments may greatly influence resin related GHG differences;
- The below analysis is not an attempt to offer an exhaustive explanation, but rather to present how a range of likely end-of-life possibilities might affect resin related GHG profiles.
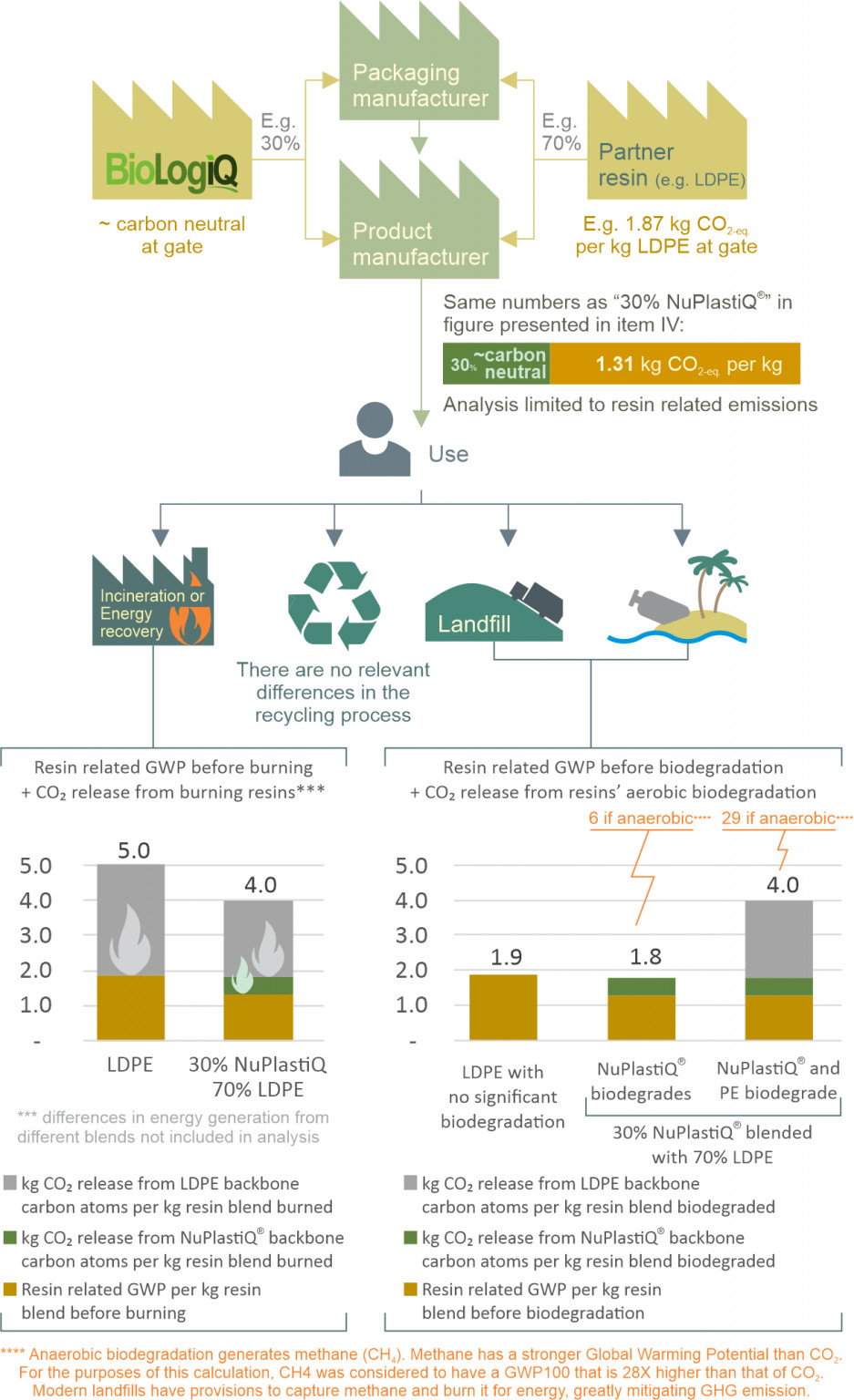
Takeaways:
- In the incineration scenario, very common in Western Europe and Japan, NuPlastiQ® blended with LDPE is GHG advantaged over the pure LDPE counterpart;
- In the recycling scenario, no significant resin-induced differences are expected in the GHG profile. Carbon atoms from the different blends remain in the respective backbones. No significant differences expected in the recycling process itself (e.g. water and energy for washing, energy for pelletizing, etc.);
- Landfill and environmental leakage scenarios share a common factor regarding resin related GHG differentiation; Biodegradation.
- LDPE (similarly to other polyethylene families, polypropylene or polystyrene) is known to biodegrade very slowly even under ideal conditions, with negligible emissions in the first 100 years (GWP100). LDPE, therefore, is not expected to “grow” its GWP100 footprint in landfills or when leaked to the environment.
- NuPlastiQ blended with LDPE will have its carbon footprint affected by the biodegradation conditions:
- If the condition is not prone to biodegradation (e.g. paper not biodegrading in a given landfill), the blend will keep its carbon atoms and the GHG profile will be unaffected;
- If the condition is prone to biodegradation, such as defined in an ASTM D5338 setting, the entire blend (NuPlastiQ and LDPE) could biodegrade. In this case, NuPlastiQ blended with LDPE would have a disadvantaged GHG profile if compared to pure LDPE. But it would also have performed an additional function (e.g. mitigation of environmental leakage), rendering the GHG comparison less relevant due to comparing systems with different functions;
- A “partial” scenario has been added limiting biodegradation to only the NuPlastiQ portion of the blend (LDPE in blend would not biodegrade). While BioLogiQ hasn’t seen experimental evidence to support such scenario, it has been included for curiosity purposes.
VI. Summary
- NuPlastiQ® offers significant cradle-to-gate GHG benefits when blended with fossil-based resins;
- NuPlastiQ maintains its GHG advantage in controlled end-of-life scenarios, such as incineration, recycling and landfills with methane capture;
- NuPlastiQ and LDPE (or other polyolefin) BioBlends will have a disadvantaged GHG profile (compared to pure polyolefin) if biodegradation occurs in uncontrolled environments such as the soil or ocean. But a disadvantaged GHG profile is expected when looking at a biodegradable product against one that isn’t biodegradable. At this point, a fair comparison would look at the blend in question compared to other viable technologies to mitigate environmental leakage and persistence.
A Story Worth Telling
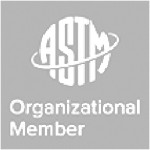
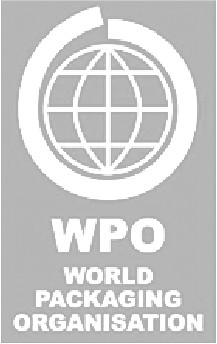
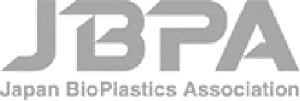

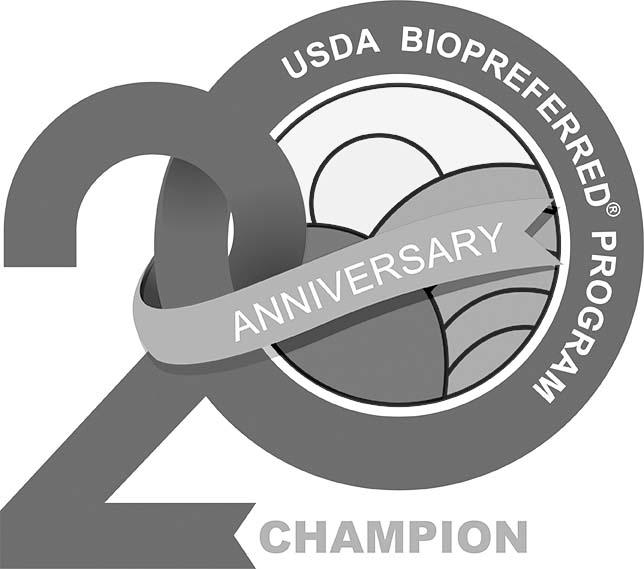
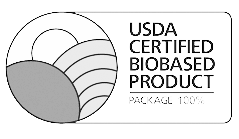
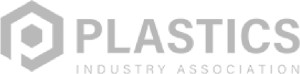
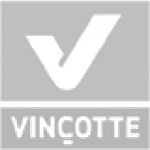
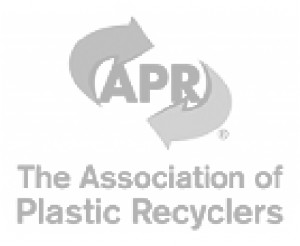
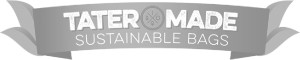